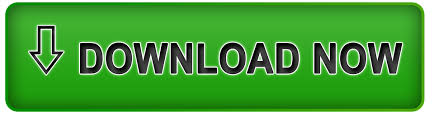

- #Solidworks flow simulation thermal joint software#
- #Solidworks flow simulation thermal joint series#
The results are nearly the same, where the main difference can be attributed to choosing different material properties from the available materials in each program more specifically Flow Simulation has, out of the box, temperature-dependent properties for copper and solder. The results from both are shown in Image 2.
#Solidworks flow simulation thermal joint software#
Both Simulation Professional and Flow Simulation can be run as either steady-state or transient problems.Īn example model of a regulator microchip was set up in both software packages running the heat conduction problem and convection applied as a boundary condition. There is an option to solve a problem for Heat Conduction in solids only, as shown in Image 1, so the flow equations are ignored and it only solves the energy equation. We can say that for conduction only, Flow Simulation is at least equivalent to Simulation Professional’s capabilities. The question that I would want to consider in choosing Simulation Professional Thermal solver as my heat transfer analysis solution is whether solving conduction only is applicable in all cases.

One of the nice outcomes of this is that for Conduction, the unknown quantity solved for is the temperature where subsequent calculations are done to get the strain and stress values that are wanted.] So in conclusion, the Simulation Professional Thermal solver is perfect suited for solving the conduction heat transfer problem, but convection and radiation can only be applied as known boundary conditions. So for conduction can be solved in the same way as for elastic displacement. One can notice that the equation for solving the linear steady-state thermal conduction in matrix format, using the method employed by the Simulation Professional solver, fits the same exact pattern as that for Hooke’s Law used in linear structural stress analysis. The solver in Simulation Professional should be thought of as the “Conduction heat transfer thermal solver,” though “Thermal” is used for short.Ĭonduction occurs in both fluids and solids through a temperature difference by electrons moving within the carrier material.
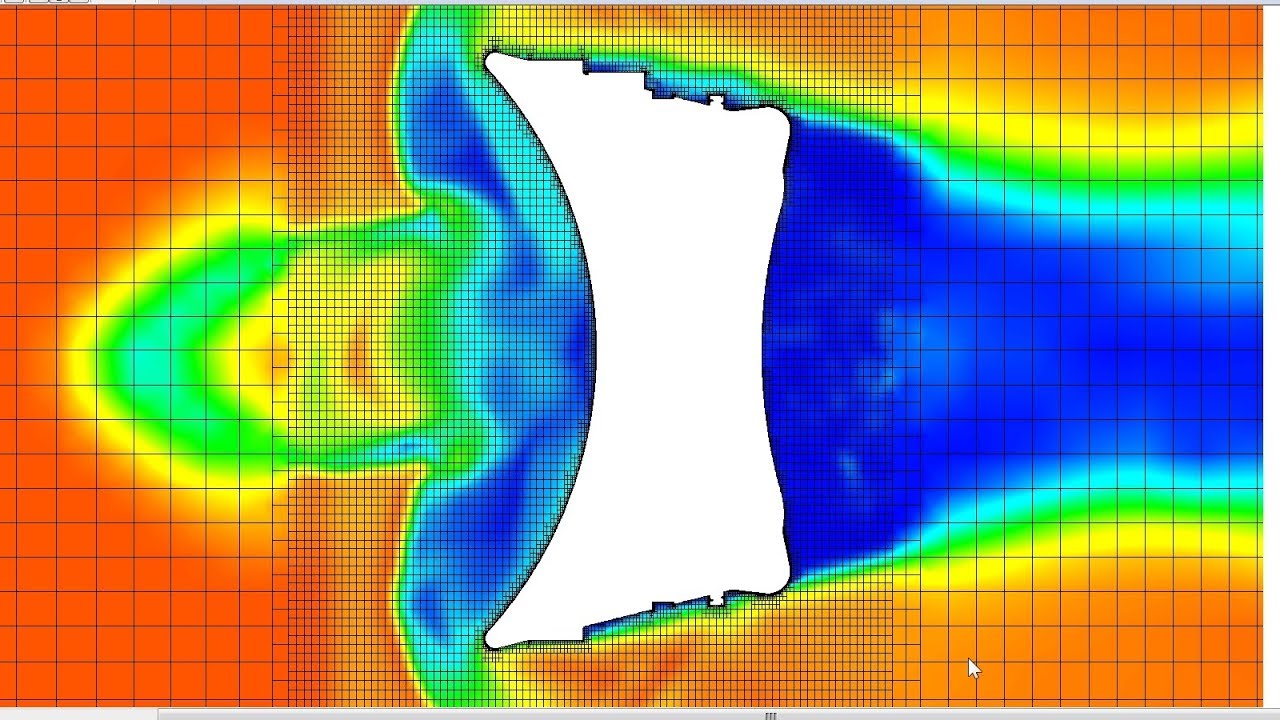
I’ve made a long-form video explaining all of these modes in more detail, see link at the bottom, so I will only summarize them here in the series.
#Solidworks flow simulation thermal joint series#
The main 3 reasons why Flow Simulation is the better option will be outlined in a series of three parts.Īs noted above, there are three modes of heat transfer: conduction, convection and radiation. The most typical exceptions would be when: (1) there is no convective heat transfer mechanism in the problem that is being solved because likely the object(s) are in a vacuum and only transport heat through conduction and radiation or (2) the thermal solution does not require a great deal of accuracy reflecting a physical test perhaps in the very early design stages when estimates are sufficient. With the exception of very few scenarios, when considering a thermal analysis solver for SOLIDWORKS, you should choose to use Flow Simulation, which is a computational fluid dynamics (CFD) code. For thermal heat transfer analysis, choose SOLIDWORKS Flow Simulation over the Thermal solver in Simulation Professional, Part 1 of 3 Conduction
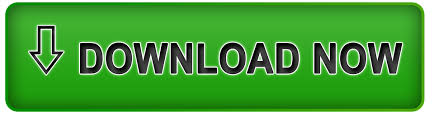